研究開発型企業の富士加飾㈱は、2次加工性を考慮した第2世代のリサイクル炭素繊維の量産設備の稼働に伴い、令和3年1月より商品名「コバトロン™」コンパウンドを商品化し、事業を開始する。
令和1年3月の環境省のリサイクル炭素繊維の実証事業終了と環境省による成果の認定を受け、環境省の補助金で兵庫県小野市に総額3億円の事業化量産設備の投資を行い、令和2年9月に設置を完成した。
令和2年10月20日、21日に神戸市で開催される令和2年度ひょうご次世代産業高度化プロジェクト「エンジンフォーラム神戸2020」に設備の全容と回収rCFサンプル、コンパウンド商品群を初公開すると共に今後の事業化スケジュールを提示する。
令和2年10月22日に大阪市本町の産創館で開催される(SDGs対応技術展2020)に引き続き出展する。
炭素繊維強化の対象樹脂は、6ナイロン、9Tナイロン、PES、LCPと多岐にわたっており、繊維含有率は30~50wt%と広範囲に対応が可能である。
販売に関しては、コバトロン™ブランドで直接市場に販売するが、同時に各原料メーカーにOEM供給し、rCF強化樹脂シリーズとして既存のコンパウンドのラインアップに追加することも検討中で、販売力強化に結び付ける。
25㎜チョップストランドでrCF価格が安価に供給できることから、6ナイロンの30%rCF強化グレードは800円~1000/kgで販売予定。rCFを独自のコンパウンド技術で開発した結果、機械的性能は新品炭素繊維を用いた従来品と同等でありながら、価格は50%以下に抑えることができる。
生産規模としてリサイクル設備は当面、日量500Kg、月産10トン程度からスタートし、CFRP端材の入荷状況を確認しながら、現状設備で月産50トン程度まで増産する。
2軸コンパウンドラインは、日量5トン、月産100トン程度の能力を持つことから受注量に応じて稼働体制を調整する。
量産にかかるリサイクル源は、現在は製造時に発生する端材(ポストインダストリー)を用いているが、今年度以降、使用済みの厚肉の水素ボンベや、使用済み航空機部材等のポストコンシューマーまで範囲を広げていき、将来の需要拡大に備える。
これまで開発されてきたリサイクル設備は、海外も含めて殆どが破砕による小片化が前提となるが、厚肉のCFRPや、大型部材は破砕処理が困難であり、コストもかかるため敬遠されている。今回完成したリサイクル回収設備は反応部が、幅2.5m、高さ2.0m、奥行き3.0mで、層内が高速気流で撹拌され、乾留(蒸し焼き)反応が大型部品でも均一に行われるため被処理材の、サイズ、板厚に制限がなく、組み込まれた金属部品やガラスクロスは、次工程での分別が容易であり、塗装膜も分解除去できるため、高純度(96~98wt%)の炭素繊維が取り出せる。また、残留した2~4%の成分はマトリックス樹脂由来のカーボンであり、コンパウンド樹脂の性能には影響しない。
本技術は、応用範囲が広く、精度も高いため、リサイクルの目途のないCFRPを使用した退役航空機や廃自動車の様な大型で、厚肉あるいは金属部品やガラスクロスが組み込まれたCFRP製品も処理できる量産設備である。この技術の幅広い適用によって、炭素繊維のサーキュラーエコノミーを成立させる世界初のチャレンジが可能になる。
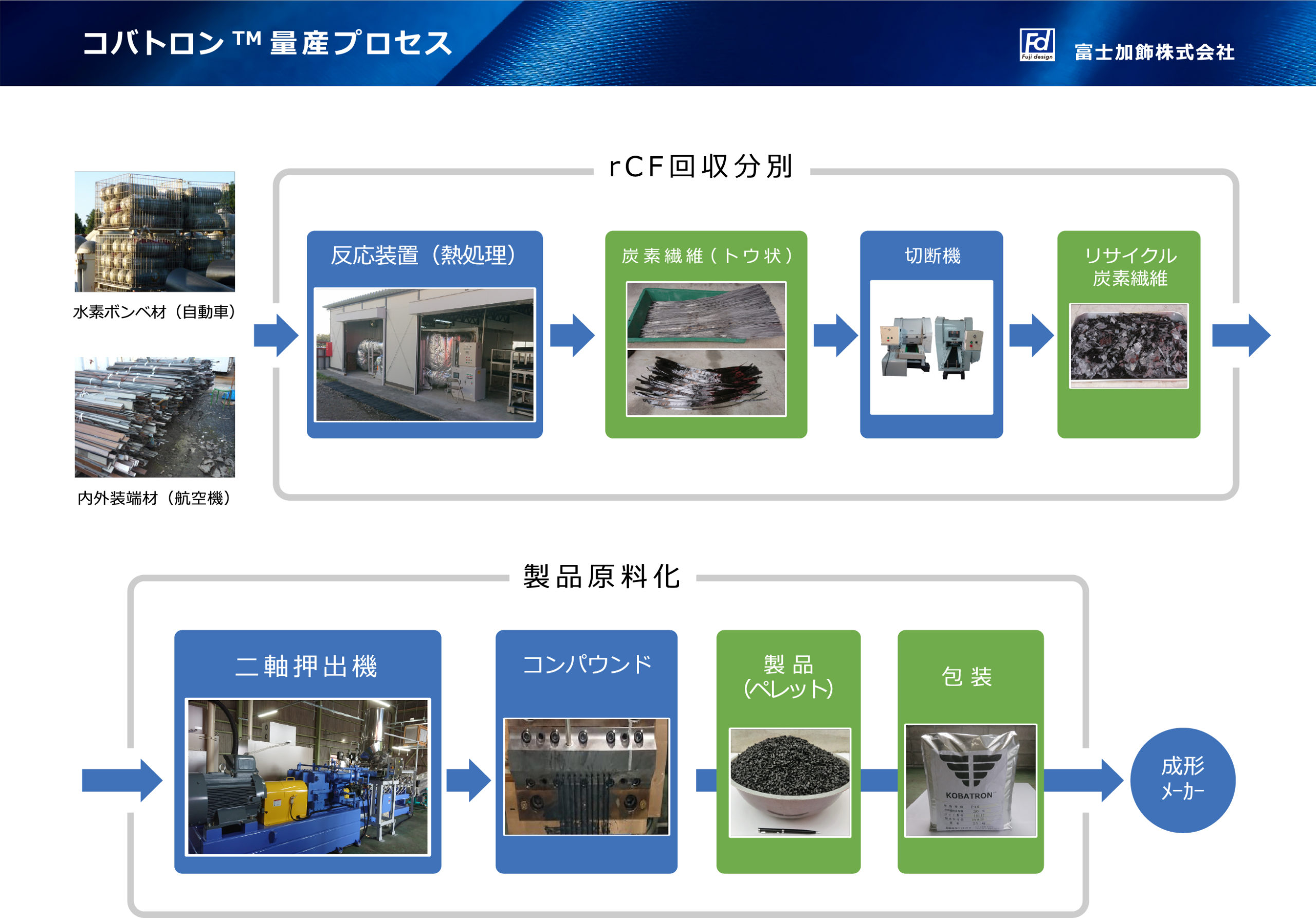
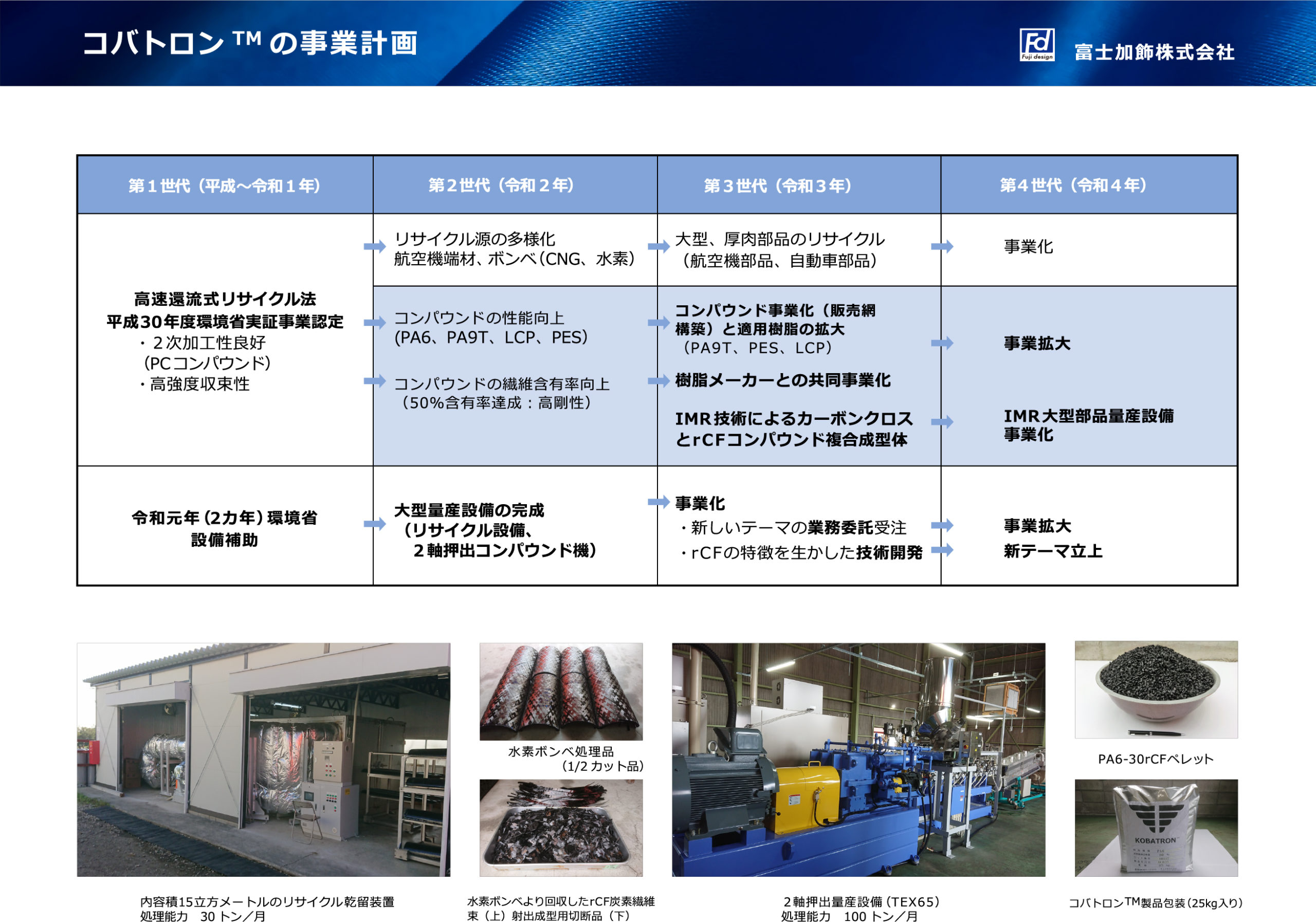
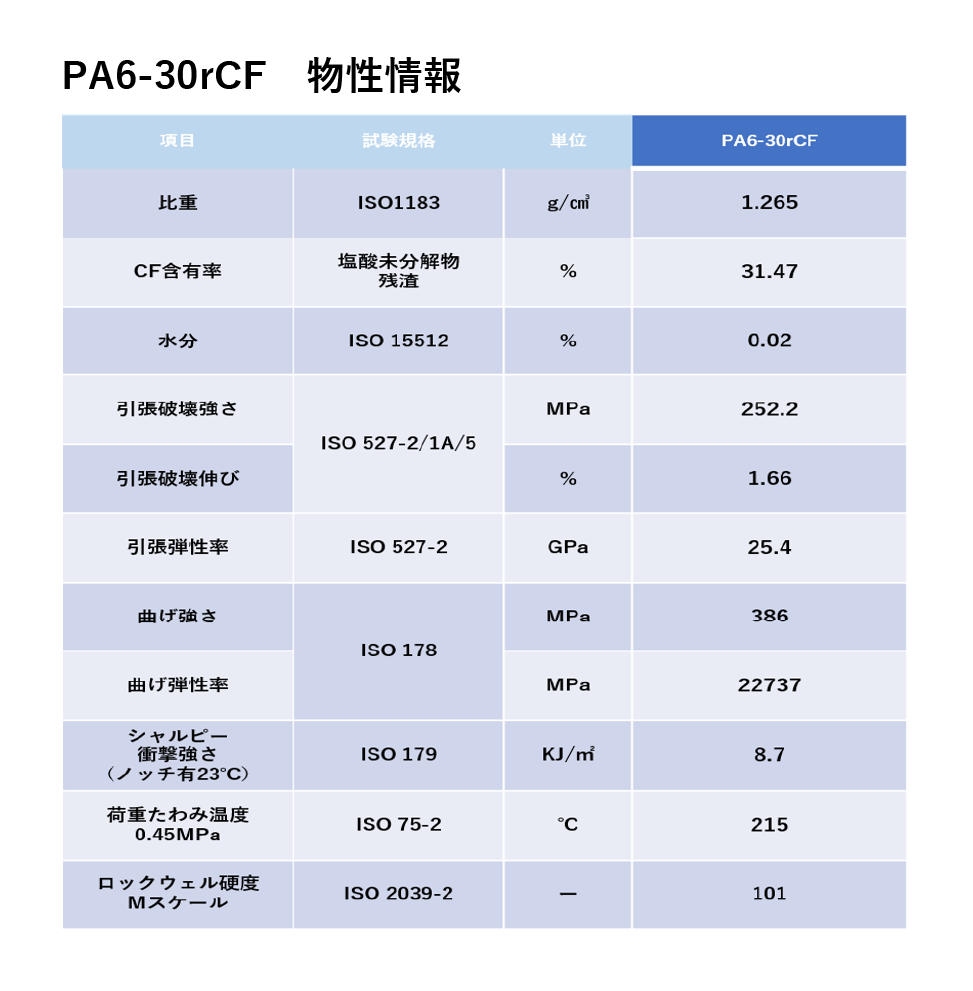